Wednesday, May 11:
Using simple addition, I calculated the position of the new window sill by working my way down from the ceiling:
- Space above the new window header: 5 3/4"
- Height of new window header: 7 1/4" (the thickness of a 2x8 triple-beam)
- Height of window opening: 48 3/4" (allowing some wiggle room at the top and bottom)
- Thickness of window sill plate: 1 1/2" (the thickness of a 2x6)
Total: 63 1/4"
Why 5 3/4" above the window header? Because I am going to install the new header slightly below the temporary beam that is currently supporting the ceiling/roof. That beam (see previous post) is made of 2x6's
– which are 5 1/2" tall. The new window header will be 1/4" lower
– that way I can easily pull the temporary beam out of there once the permanent header is holding everything up.
I measured the
63 1/4" down from the undersurface of the top wall plate and placed a mark on the wall. The old, existing undersill stud on the right end was all ragged and split up with nails, so I pried it out and installed a new 2x6 stud that came up to the mark for the right-end of the window sill. (For the left-end of the sill, I simply sawed off the top of the existing old stud at the correct level.)
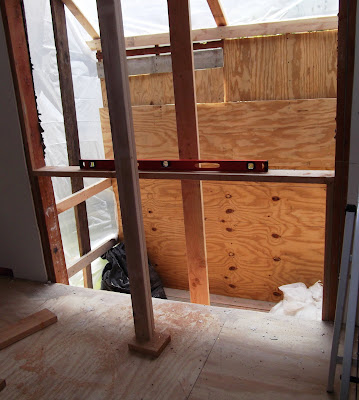 |
Above and below: Making sure the two ends of the sill are level. Prior to actually nailing the sill and installing the studs below it, I need to drag the new window from the upstairs office through this huge opening – out onto the scaffold. (Windows are always installed from the outside of the house) |
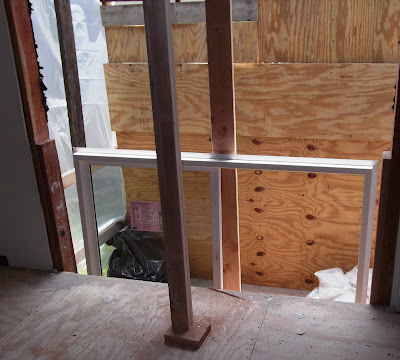 |
The window was a custom-order from Lowe's. It is a "Milgard," with double-pane low-E glass in a strong vinyl frame – excellent quality and value (probably 1/3 the cost of an Andersen window). To make it lighter, I removed the sliding portion and then muscled it out onto the scaffold. |
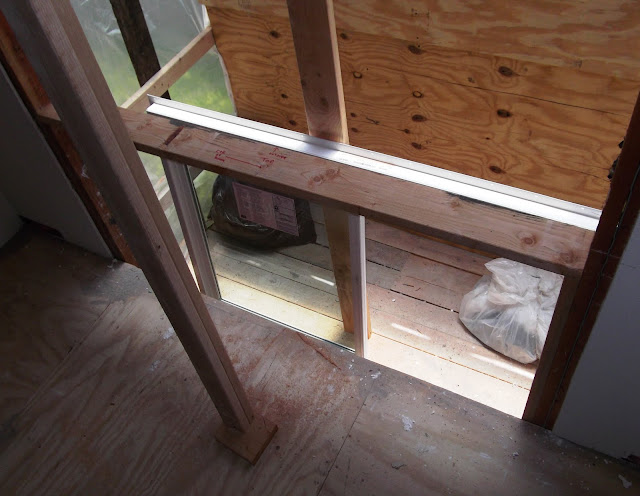 |
Now that the window is on the outside, I can frame the wall. (The white plastic bundle on the outside scaffold contains all the broken glass from the old plate-glass window. The black bag is full of stucco debris. Once the trash is collected Thursday, I plan to push these heavy bundles off the end of the scaffold – bombing them directly into the trash cart. Managing the waste on a construction job sometimes entails as much planning as the actual construction!) |