Since my last post, I have spent some time plastering walls. Taping, floating and texturing sheetrock does not make for exciting visuals, but it does have the tendency to transform a room if it's done well.
The addition of the Tea Room affected the adjacent office wall and the downstairs dining room. My goal has been to get those two side-projects done prior to finishing the Tea Room.
This week, after multiple coatings of drywall compound and some light sanding, I put the final coat of paint on the office wall, which once had an interior opening that overlooked the dining room.
Below, a sequence of photos in reverse order:
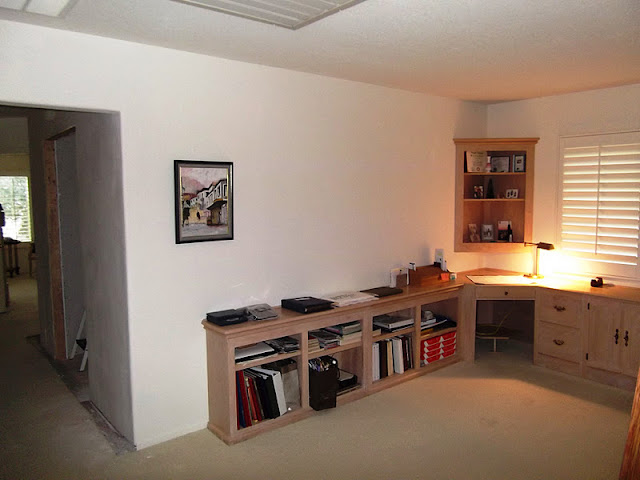 |
The finished office wall, with its first piece of artwork – an oil of a Maltese street scene –
painted by Anne's uncle, Ted Burke, about a half-century ago.
Below: A reverse sequence that shows how it looked before. |
As I neared completion of the office wall, I was finally inspired to tackle the dining-room ceiling, which is, by far, the hardest finishing job I face.
Below: Some photos of taping and floating.
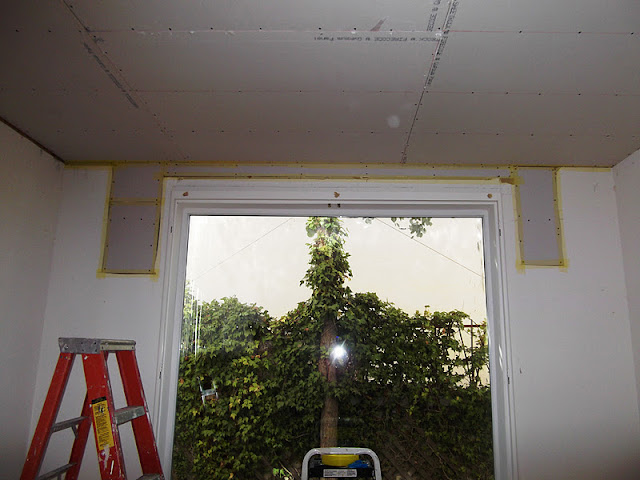 |
When I cut away the upper part of the plantation shutters 6 months ago, I made no effort to get a clean, finished cut across the wood frame. The shutters ran upward into a vaulted ceiling – I just wanted to get them out of my way so that I could build the new upstairs Tea Room.
But last week, prior to taping and floating around the window, I used my circular saw to make a clean cut across the top of the frame. I screwed a 1x3 board onto the wall to use as an edge-guide, put a diamond-tipped "Diablo" finishing blade onto the saw, and then dragged the saw horizontally across the top of the frame for a perfectly straight, smooth cut.
Once the walls are finished, all I need to do around the window is touch up the paint on the shutters and re-hang them. |
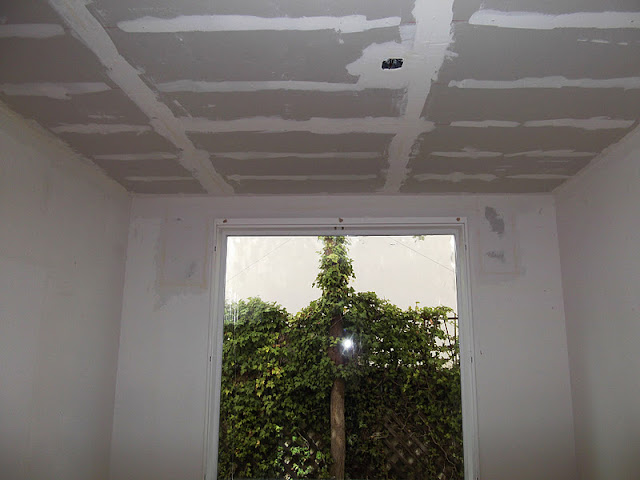
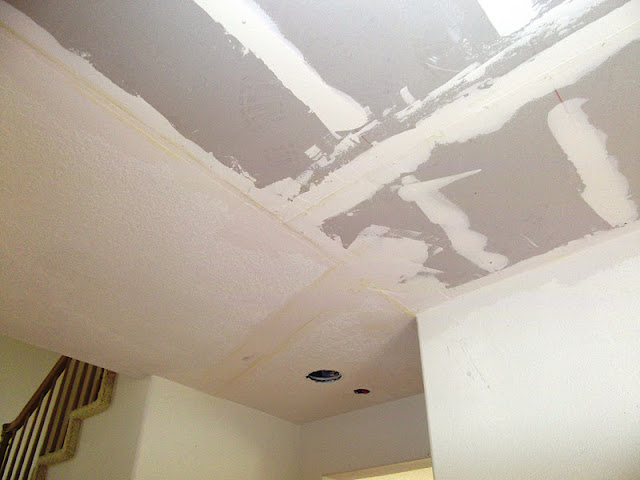 |
One of the trickiest parts will be blending the new ceiling (right) into the existing ceiling (left) – the underside of the original bridge. I will need to trowel heavy amounts of drywall compound across the seam and feather it out widely.
From years of experience, I have learned that it is much easier to apply repeated coats to achieve a smooth finish rather than trying to do a huge sanding job. |